Contents
1. 납땜 품질이 전자기기 신뢰성에 미치는 영향
전자기기의 작동 안정성은 단순히 부품 성능이나 회로 설계만으로 보장되지 않습니다.
눈에 보이지 않는 납땜 품질이 전체 시스템의 신뢰성에 결정적인 영향을 미치는 핵심 요소입니다.
특히 고집적·고속화가 가속화되는 현대의 SMT(Surface Mount Technology) 환경에서는 납땜 불량의 종류도 점점 더 다양해지고 있으며, 이로 인한 품질 리스크 역시 크게 증가하고 있습니다.
1-1) 납땜(전기적 연결과 기계적 고정)
납땜은 단순히 전기를 흐르게 하는 역할만 하는 것이 아닙니다.
부품과 회로 패드를 전기적으로 연결할 뿐만 아니라, 기계적으로도 단단히 고정시켜 외부 충격이나 진동에도 견딜 수 있게 합니다.
예를 들어 BGA, QFN과 같은 미세패키지 소자는 솔더볼이나 솔더 패드 위에 정확하게 위치하지 않으면 열이나 전류에 취약해지고, 결국 동작 불량을 일으킬 수 있습니다.
따라서 납땜은 ‘붙였다’는 사실보다 얼마나 잘 붙였는가, 다시 말해 ‘납땜 품질’이 더 중요합니다.
1-2) 고장과 직결되는 SMT/PCB 환경
최근의 SMT 기반 전자기기는 부품 크기가 작고 핀 간 간격(Pitch)도 매우 좁습니다.
이처럼 미세한 패턴에서는 아주 작은 결함 하나도 치명적인 문제로 발전할 수 있습니다.
예를 들어, 육안으로 식별이 어려운 미세 보이드(Void), 냉땜, 크랙과 같은 납땜 불량의 종류는 시간이 지나면서 열화나 개방(Open Fault), 간헐적 접촉 문제를 일으킬 수 있습니다.
또한 온도 변화나 진동, 반복된 ON/OFF에 의해 솔더 접합부에 스트레스가 반복되면, 솔더 피로(Solder Fatigue)에 의한 크랙이 발생하고, 이는 장기적인 신뢰성 문제로 이어집니다.
특히 FPC, 고전류 회로, 고주파 설계에서는 이러한 납땜 결함이 설계 의도와 다른 동작을 유발할 수 있습니다.
1-3) 납땜 불량 주요 사례 (열화, 개방, 단락 등)
실제 현장에서는 납땜 불량의 종류에 따라 다양한 문제들이 발생합니다.
- 브리지(Solder Bridging): 인접 패드 간 납이 연결되며 단락(쇼트)이 발생
- 냉땜(Cold Solder): 납이 충분히 녹지 않아 접촉 불량 또는 접합강도 저하
- 보이드(Void): 내부 기포로 인한 전류 흐름 저하 또는 열 저항 증가
- 크랙(Crack): 솔더 피로로 인한 미세 균열 → 개방(Open) 또는 불안정 동작
- 이온성 오염/플럭스 잔류물: 표면 누설전류, 부식, 장기적 열화 유발
전자기기에서 발생하는 고장의 상당수는 겉으로는 보이지 않는 아주 미세한 결함에서 비롯됩니다.
특히 PCB 제조 및 SMT 조립 공정에서 자주 언급되는 납땜 불량은, 단순한 공정 실수 이상의 문제로 취급됩니다.
이 중에는 겉보기에는 납땜이 정상적으로 이루어진 것처럼 보이지만, 실제로는 내부 접합 강도가 낮거나 장기 신뢰성에 영향을 주는 경우도 있습니다.
대표적인 예로, 솔더 페이스트(크림솔더)의 인쇄 과정에서 패턴의 모서리나 함몰된 부분처럼 지형적으로 열과 플럭스가 집중되기 어려운 영역에서는 납땜이 충분히 퍼지지 않고 고르게 도포되지 않는 경우가 많습니다.
이런 경우 습윤성이 떨어지며, 그 결과 보이드(Void)나 접합 불량이 발생할 수 있습니다.
이처럼 납땜 불량의 종류 중에서 납땜 불량은 고장의 직접적인 원인이 되며, 눈에 보이지 않기 때문에 더욱 위험합니다.
납땜 불량의 종류 중에서 납땜 품질을 평가할 때 자주 등장하는 개념이 바로 ‘습윤성(Wettability)’입니다.
이는 용융된 납이 기판이나 부품의 표면에 얼마나 잘 퍼지고 밀착되느냐를 의미하는 특성입니다.
기술적으로는 접촉각(Contact Angle)이라는 개념으로 정의되며, 납방울이 금속 표면 위에 놓였을 때 형성되는 각도를 통해 습윤성을 판단할 수 있습니다.
접촉각이 작을수록 납이 표면에 잘 퍼지며 습윤성이 높다고 평가됩니다.
반대로, 각도가 크면 납이 표면을 튕겨내는 듯한 형상이 되어 습윤성이 떨어지고 접합 강도 또한 저하됩니다.
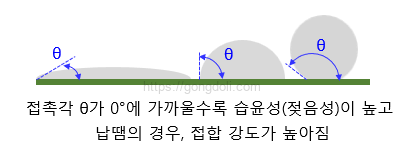
납땜 불량의 위험성은 단순히 단락(브리지)이나 개방(Open) 같은 눈에 보이는 불량에만 국한되지 않습니다.
보이드, 냉땜, 미세 크랙 등은 외관상 문제가 없어 보일 수 있지만, 실제 사용 환경에서 열, 진동, 반복된 스위칭에 의해 점차 문제를 일으키게 됩니다.
이러한 납땜 불량의 리스크를 줄이기 위해서는, X-ray 검사기나 고배율 디지털 현미경 등을 활용한 납땜 상태의 정밀 관찰과 해석이 매우 중요합니다.
특히 SMT 공정의 고속화와 부품의 소형화가 가속되는 지금은, 현미경 분석 없이는 품질 개선이 사실상 불가능한 상황입니다.
납땜 불량은 단순히 공정 중의 문제로 끝나는 것이 아니라, 전자기기의 수명과 안정성을 결정짓는 핵심 품질 요소입니다.
그 중에서도 습윤성 저하는 눈에 띄지 않지만 점차적으로 접합 신뢰성을 약화시키는 매우 위험한 변수입니다.
따라서 다양한 납땜 불량의 종류와 유형을 사전에 파악하고, 정밀한 관찰과 분석을 통해 원인을 정확히 이해하는 것이 품질 향상의 시작입니다.
- 연관 참조 : 납땜 불량 해결 방법, 예방 및 개선 대책,리플로우 최적화,PCB 및 패드 설계 단계 예방
- 연관 참조 : PCB 기본 개념, 용어, 구성 요소, PCB 종류, PCB 경제 치수
- 연관 참조 : PCB 방열 설계,열 저항과 방열 기본,효율적인 PCB 방열 설계
2. 주요 납땜 불량의 종류와 특징
전자기기에서 발생하는 다양한 고장 중, 상당수는 육안으로 확인하기 어려운 납땜 결함에서 비롯됩니다.
2-1) 브리지 (Solder Bridging)
납땜 불량의 종류 중에서 가장 치명적인 문제 중 하나가 바로 브리지(Solder Bridging)입니다.
브리지는 인접한 두 개 이상의 패드 또는 부품 핀 사이가 납으로 인해 의도치 않게 연결(단락)되어 쇼트(short) 상태를 유발하는 현상입니다.
특히 웨이브 솔더링(Wave Soldering) 공정에서는 이 현상이 매우 자주 발생할 수 있으며, 제조 라인에서 반드시 체크해야 할 핵심 품질 항목 중 하나입니다.
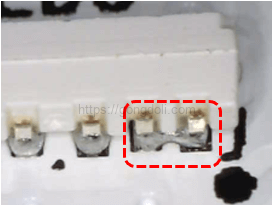
2-1-1) 브리지는 왜 발생할까?
납땜 불량의 종류 중에서 브리지는 기본적으로 납이 과도하게 흐르거나, 흐른 납이 인접 패드로 끌려가며 형성되는 물리적 현상입니다.
하지만 이 단순한 현상 뒤에는 다양한 공정상의 문제가 숨어 있습니다.
대표적인 원인은 다음과 같습니다.
- 부품 간 간격(Pitch)이 너무 좁은 경우
패드 간 간격이 설계상 지나치게 좁거나, Fine-Pitch 부품이 밀집되어 있는 경우 브리지가 발생할 확률이 높아집니다.
이는 납이 열적으로 충분히 분리되기 전에 인접 부위로 퍼지며 의도치 않게 연결되는 결과를 낳습니다. - 납땜 온도가 너무 낮게 설정된 경우
납이 충분히 용융되지 않으면 표면 장력에 의해 한쪽으로 뭉쳐 흐르게 되고, 이 과정에서 인접 핀으로 흘러들어 브리지를 형성할 수 있습니다.
특히 웨이브 납땜에서는 솔더 웨이브의 온도가 낮을 경우 납이 제대로 흘러가지 못하고 잔류하면서 단락이 발생하기 쉽습니다. - 납땜 시간이 너무 짧거나, 냉각이 너무 빠른 경우
웨이브 통과 시간이 짧으면 열 전달이 충분하지 않아 납이 제대로 용융되지 않거나 고르게 분포되지 못합니다.
반대로, 납땜 직후 급격한 냉각이 이루어질 경우, 납이 흐르는 도중에 급속하게 고체화되어 브리지가 고정될 수 있습니다. - 플럭스 분사량 부족 또는 분사 불균형
플럭스는 금속 표면의 산화를 제거하고 납의 젖음성을 높여주는 역할을 합니다.
분사량이 부족하면 습윤성이 저하되어 납이 원하는 위치에 고르게 퍼지지 않으며, 이로 인해 납이 한쪽으로 몰리며 브리지가 발생할 수 있습니다.
2-1-2) 개선 방법 (단순 조정이 아닌 공정 최적화가 해답)
납땜 불량의 종류 중에서 브리지는 단순히 납이 너무 많아서 생기는 문제가 아닙니다.
온도, 시간, 플럭스, 위치 정렬 등 다양한 공정 요소가 복합적으로 작용한 결과입니다.
다음은 브리지 발생 시 점검하고 개선할 수 있는 대표적인 방법입니다.
- 웨이브 온도 확인: 솔더 웨이브 온도를 적절하게 설정하고, 예열 구간의 온도 분포가 고르게 유지되고 있는지 확인합니다.
- 납땜 시간 조정: 기판이 웨이브를 통과하는 시간을 연장하거나, 온도 Ramp-Up 속도를 조절하여 열이 충분히 공급되도록 합니다.
- 냉각 조건 조정: 납이 천천히 응고되도록 냉각 속도를 조정하여 납이 자연스럽게 패드 위에 안착하도록 합니다.
- 플럭스 분사량 보정: 플럭스 분사 노즐이 막혀 있거나, 분사량이 부족한 경우에는 납땜 균일성이 떨어지므로 노즐 정비 및 분사 프로파일을 조정해야 합니다.
- 부품 위치 보정: SMT Pick & Place 단계에서 부품이 정확한 좌표에 배치되지 않으면 납이 인접한 패드로 흘러들 수 있습니다.
→ 카메라 좌표와 실제 기판 위치 정합을 재점검해야 합니다.
브리지는 단순한 납땜 불량의 한 종류가 아니라, 전체 생산 품질에 치명적인 영향을 미치는 결함입니다.
설계와 공정이 복잡해지는 현대 SMT 환경에서는 납땜 불량의 종류가 다양화되고 있으며, 브리지는 그 중에서도 전기적 단락이라는 치명적인 고장을 유발할 수 있는 가장 위험한 결함 중 하나입니다.
이러한 브리지를 방지하려면, 단순히 납땜 조건을 조정하는 것만으로는 부족합니다.
공정 전체를 통합적으로 이해하고, 각 요소를 정밀하게 제어하는 품질 시스템이 필요합니다.
2-2) 보이드 (Solder Voiding)
납땜 불량의 종류 중에서도 보이드(Void) 또는 기공(Porosity) 현상은 외관상 쉽게 드러나지 않지만, 내부에서 전자기기의 신뢰성과 수명을 잠식하는 매우 위험한 결함입니다.
보이드는 용융 납이 응고되는 과정에서 가스가 빠져나가지 못하고 납 내부에 빈 공간으로 갇히는 현상을 말합니다.
이는 고전류 회로나 열전달이 중요한 소자에서 전기적, 열적, 기계적 성능 저하를 유발할 수 있습니다.
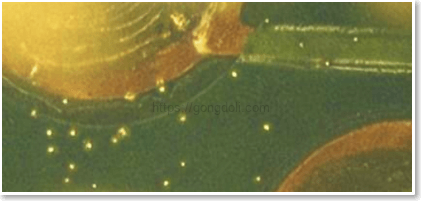
2-2-1) 보이드란 무엇인가?
납땜 불량의 종류 중에서 보이드(Void)는 말 그대로 ‘빈 공간’을 의미합니다.
납땜이 이루어진 접합부 내부에 기체(주로 플럭스 증기나 수분 증기)가 빠져나가지 못하고 갇힌 상태로 응고되면서 형성됩니다.
특히 BGA, QFN, 써멀패드(히트싱크 접합용)처럼 납땜 면적이 넓고 열 전달이 중요한 부위에서 자주 발생하며, 납땜 불량의 종류 중에서도 분석과 개선이 까다로운 편입니다.
2-2-2) 보이드가 발생하는 이유
- 가스 방출 불량
납땜 과정 중 플럭스가 열에 의해 분해되면서 발생하는 가스가 납 내부에 갇히는 경우 보이드가 형성됩니다.
웨이브 납땜 시 솔더 웨이브와의 접촉 시간 또는 온도가 부적절하면 가스가 빠져나가지 못하고 내부에 기포로 남게 됩니다. - 표면 오염물질
납땜 패드나 부품 리드에 산화물, 기름, 먼지, 플럭스 잔류물 등이 남아 있는 경우, 납이 제대로 젖지 않으며 이로 인해 가스가 형성되거나 고르게 퍼지지 않아 기공이 발생합니다. - PCB 또는 부품의 수분 잔류
PCB 또는 부품 내부에 남아 있는 수분은 고온의 리플로우나 웨이브 통과 시 갑작스럽게 팽창하면서 Popcorn Effect를 유발하고, 내부에서 가스가 생겨 보이드를 만들어냅니다. - 부적절한 도금 상태
통과 홀(Through Hole) 납땜에서 내벽 구리 도금이 얇거나 불균일할 경우(25µm 미만), 납이 홀 벽을 따라 균일하게 올라가지 않으며 기공이 생기기 쉬운 구조가 됩니다.
2-2-3) 보이드가 유발하는 문제
- 전류 통로 감소 → 저항 증가, 발열 유발
- 열 전달 방해 → 발열 소자에서 열 축적
- 접합 강도 저하 → 크랙 및 피로 파손
- 간헐적 오작동 → 고장 분석이 어려운 Random Fail
이러한 문제는 제품 초기에는 드러나지 않지만, 수개월 내지 수년 뒤에 예상치 못한 고장으로 이어질 수 있는 전형적인 신뢰성 문제입니다.
따라서 납땜 불량의 종류 중 보이드와 기공은 반드시 사전 관찰 및 제어가 필요합니다.
2-2-4) 보이드 개선 방안
- 납땜 표면 세정 강화
납땜 전에 PCB 표면 및 부품 리드를 철저히 세정하여 산화물, 기름, 불순물을 제거합니다. - 플럭스 최적화
고잔류성 플럭스 사용을 지양하고, 휘발성과 습윤성이 우수한 플럭스를 선택합니다. - 리플로우/웨이브 온도 프로파일 조정
예열 단계에서 충분한 가열과 탈기(De-gassing)를 유도하고, 급속 냉각은 피해야 합니다. - 부품 및 PCB 사전 건조 (Bake Out)
수분 잔류 방지를 위해 125°C에서 12~24시간 건조 후 작업합니다. MSD 관리 필수. - Through Hole 도금 품질 확보
웨이브 납땜 시, 구멍 내벽에 최소 25µm 이상의 구리가 도금되어야 납이 고르게 올라가고 기공을 방지할 수 있습니다.
보이드 납땜 불량의 종류 중에서 가장 은밀하지만 치명적인 문제입니다.
특히 웨이브 납땜이나 수작업 납땜에서는 가스 방출, 표면 오염, 플럭스 선택, 온도 제어와 같은 세부 공정 요소가 보이드 발생에 큰 영향을 미칩니다.
이러한 문제를 사전에 예방하고 줄이기 위해서는 정밀한 공정 관리와 납땜 분석 시스템의 구축이 필수적입니다.
2-3) 냉땜 (Cold Solder Joint)
전자기기 제조 현장에서 발생하는 납땜 불량의 종류 중 가장 교묘하고 위험한 유형 중 하나가 바로 냉땜(Cold Joint)입니다.
냉땜은 말 그대로 납이 충분히 녹지 않거나, 냉각 과정에서 제대로 응고되지 못한 채 기계적, 전기적 접합이 불완전하게 형성된 상태를 의미합니다.
외관상으로는 울퉁불퉁하거나 무광택의 거칠고 흐릿한 표면을 가지며, 때로는 정상적인 납땜과 육안 구분이 어려운 경우도 있어 더욱 문제가 됩니다.
2-3-1) 냉땜이란 무엇인가?
납땜 불량의 종류에서 냉땜은 다른 표현으로 냉납, 또는 단순히 납땜 불량이라고도 불리며, 일반적인 양질의 납땜처럼 표면이 매끈하고 광택이 있는 것이 아니라, 뿌옇고 불규칙한 자국이 남아 있는 것이 특징입니다.
냉땜 상태에서는 납이 금속 패드나 리드에 완전히 젖어들지 못해 전기적 접촉 면적이 줄어들고, 기계적으로도 약하게 고정되어 있어 진동, 열변형, 반복 스트레스에 쉽게 파단될 위험이 있습니다.
이러한 냉땜은 납땜 불량의 종류에서 대표적인 사례로서, 초기 검사에서는 통과되지만 제품 사용 중 접촉 불량을 일으켜 몇 달 또는 몇 년 뒤에야 문제가 드러나는 경우도 많습니다.
2-3-2)냉땜이 발생하는 주요 원인
냉땜은 일반적으로 웨이브 납땜(Wave Soldering), 수작업 납땜, 리플로우 납땜 등 거의 모든 납땜 공정에서 발생할 수 있으며, 주요 원인은 다음과 같습니다.
- 납땜 온도가 너무 낮을 때
납이 충분히 녹지 않으면 금속 표면에 제대로 퍼지지 못하고 표면장력으로 인해 뭉치게 됩니다.
이로 인해 젖음성(Wettability)이 저하되어 접합 강도가 떨어지는 냉땜이 발생합니다. - 체인 속도가 너무 빠를 때 (웨이브 납땜의 경우)
PCB가 솔더 웨이브를 너무 빠르게 통과하면 납과의 접촉 시간이 부족하여 용융 및 접합이 불완전하게 이루어집니다.
이는 곧 납땜 불량의 대표적 사례인 냉납을 유발하게 됩니다. - 냉각 중 진동이나 외력 작용
납이 아직 응고되지 않은 상태에서 체인 진동, 공정 상 충격, 작업자의 손동작 등으로 인해 접합부가 흔들리면, 납이 흐르지 못하고 응고되어 표면에 주름이 생기거나 들뜸 현상이 발생합니다. - 부품 및 패드 표면의 산화
산화된 금속 표면은 납과 잘 접합되지 않기 때문에, 아무리 납이 녹아도 젖음성이 떨어지고 냉땜으로 이어질 가능성이 매우 높습니다.
2-3-3) 냉땜이 유발하는 문제
냉땜은 납땜 불량의 종류 중에서도 진단이 늦게 이루어지는 경우가 많은 결함입니다.
다음과 같은 형태의 문제를 유발할 수 있습니다.
- 간헐적인 접촉 불량: 진동 또는 열 변화 시 연결이 끊겼다가 다시 붙는 현상이 반복됨
- 저항 상승 및 과열: 접합 면적이 좁아지면서 국부 발열 발생
- 전류 차단 및 회로 오작동: 내부에서 개방(Open) 상태가 발생하여 전체 회로가 동작하지 않음
- 장기적 신뢰성 저하: 초기에는 정상 작동하더라도, 수개월 내지 수년 후 고장 가능성 증가
2-3-4) 냉땜을 예방하기 위한 공정 제어 포인트
- 정확한 납땜 온도 설정
납땜 재료(Sn63/Pb37, SAC305 등)에 따라 적절한 Peak 온도 및 예열 속도 설정이 필요합니다. - 체인 속도 및 웨이브 접촉 시간 최적화
웨이브 납땜의 경우 납땜 시간과 속도는 제품 및 보드 두께에 맞춰 정밀하게 조정해야 합니다. - 진동/충격 방지
냉각 중 보드를 고정하거나, 체인 진동을 최소화하여 냉땜을 방지합니다. - 부품 표면과 PCB 패드의 산화 방지 및 세정 유지
산화 방지를 위해 저장 환경을 관리하고, 작업 전 세정 공정을 통해 표면 청결도를 확보합니다.
냉땜(Cold Joint)은 납땜 불량의 종류 중 가장 진단이 어려우면서도 치명적인 고장을 유발할 수 있는 결함입니다.
특히 웨이브 납땜, 수작업 납땜 등에서는 온도, 시간, 진동과 같은 미세한 변수로도 쉽게 발생할 수 있으며,
초기 검사를 통과했더라도 장기적인 신뢰성에 심각한 문제를 일으킬 수 있습니다.
따라서 납땜 품질을 관리할 때는 냉땜을 단순한 ‘외관 문제’가 아니라, 제품 수명 전체에 영향을 주는 중요한 납땜 불량의 하나로 인식하고, 사전에 적극적으로 예방하고 분석하는 체계적인 접근이 필요합니다.
2-4) 크랙(Crack)과 필렛 리프리플로우(Fillet Lift)
전자회로의 신뢰성 문제는 겉으로 보이는 큰 결함보다, 눈에 보이지 않는 미세한 균열에서 시작되는 경우가 많습니다.
납땜 불량의 종류 중 대표적인 사례가 바로 크랙(Crack)과 필렛 리프리플로우(Fillet Lift) 현상입니다.
이들은 모두 납땜 접합부가 외부 스트레스나 열적 팽창, 제조 공정 중 잔류 응력 등에 의해 손상되면서 나타나는 불량입니다.
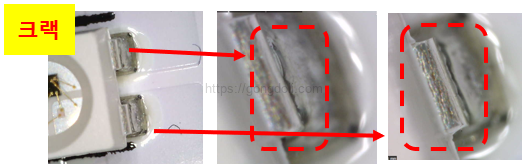
2-4-1) 크랙(Crack)이란?
크랙은 납땜 접합부에 생긴 미세한 균열을 말합니다.
일반적으로 육안으로 확인하기 어렵고, 고배율 현미경이나 X-ray, 또는 단면 분석(Cross Section)을 통해 확인됩니다.
납땜 불량의 종류 중에서도 특히 장기적인 열 스트레스나 반복 진동이 있는 환경에서 제품 수명 중 뒤늦게 고장을 유발하는 “지연형 불량”입니다.
2-4-2) 크랙의 주요 원인
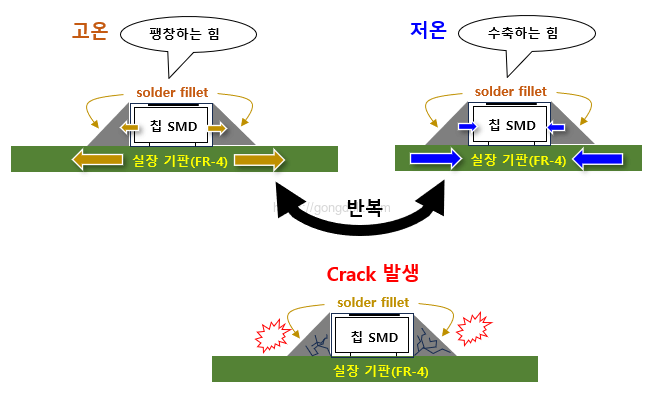
- PCB와 부품 간의 열팽창률 차이 (CTE mismatch)
납땜 접합부가 반복되는 온도 변화(전원 On/Off)로 인해 팽창/수축을 반복하면서, 납 내부에 피로균열이 발생합니다. - 급속 냉각 또는 리플로우 프로파일 부적합
너무 빠른 냉각 속도는 납의 결정화에 응력을 남기며, 이후 크랙으로 발전할 수 있습니다. - 기계적 외력
납땜 후 PCB 취급 과정에서의 휨(Bending), 낙하, 고정 불량 등이 크랙을 유발할 수 있습니다.
2-4-3) 필렛 리프리플로우(Fillet Lift)란?
필렛 리프리플로우는 납땜 후 솔더 필렛이 패드에서 들려 떨어지는 현상입니다.
겉보기에는 부품 리드와 납은 연결되어 있는 것처럼 보이지만, 패드와의 연결이 단절되어 전기적으로는 단선(Open) 상태일 수 있습니다.
- 납땜 전 패드 오염 또는 산화
납이 제대로 젖지 않아 필렛이 형성되더라도 패드와의 결합력이 낮아 쉽게 떨어집니다. - 과도한 플럭스 잔류물 또는 유기물
패드 표면과 납 사이에 불순물이 끼어 접합이 약해지고, 응고 후 납이 위로 들리는 형상이 됩니다. - 웨이브 납땜 시 리드의 형상 또는 진입 각도 문제
리드와 납은 잘 접합되었지만, 패드와는 접합이 되지 않은 상태로 고정되는 경우입니다.
2-4-4) 이들 불량이 유발하는 실제 문제
- 전기적 단선(Open)
필렛 리프트는 전기적으로 회로가 단절된 상태이므로 제품이 정상 작동하지 않습니다. - 간헐적 동작
크랙이 미세할 경우, 온도나 진동 환경에 따라 접촉 상태가 바뀌며 오작동을 유발합니다. - 열 팽창 시 응력 집중 → 파손 가속
반복되는 열 순환에 따라 크랙이 점점 커지며 납땜부 전체가 파손될 수 있습니다.
크랙과 필렛 리프리플로우는 납땜 불량의 종류 중에서도 미세 결함이 제품 신뢰성을 장기적으로 갉아먹는 전형적인 사례입니다.
이러한 불량은 발생 후에 즉시 드러나는 것이 아니라, 제품 사용 중 점차적으로 고장으로 발전하기 때문에 초기에 검출하고 예방하는 것이 매우 중요합니다.
2-5) 솔더볼 (Solder Ball)
전자기기 제조 공정에서 발생하는 납땜 불량의 종류 중 하나인 솔더볼(Solder Ball)은 크기는 작지만, 제품 신뢰성을 위협하는 주요 결함 요소입니다.
솔더볼이란, 납땜 공정 중 의도하지 않게 회로 기판 표면이나 부품 주변에 형성된 작은 납 구슬 형태의 입자로, 일반적으로는 수십~수백 마이크로미터(㎛) 크기를 가지며, 외관상은 쉽게 눈에 띄지 않을 수 있지만 위치와 개수에 따라 심각한 문제를 유발할 수 있습니다.
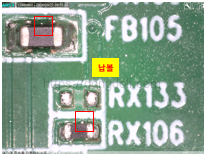
2-5-1) 솔더볼(Solder Ball)이란?
솔더볼은 주로 SMT 리플로우 납땜 공정에서 발생합니다.
- 납땜 부위 주변에 뿌려지듯 퍼져 있는 미세 구형 납 입자
- 리드 또는 패드에서 분리된 납 구슬
- 솔더 브리지와 유사하게 인접 패드 사이에 끼어있는 입자
즉, 납땜 불량의 종류중 솔더볼은 불완전한 리플로우, 플럭스 과다, 패턴 간격 불량 등으로 인해 납땜 영역에서 벗어나 불규칙하게 흩어진 납 알갱이입니다.
이는 향후 전기적 단락(Short), 절연 저하, 이온성 오염과의 연계 문제 등을 일으킬 수 있으므로 단순한 이물 수준이 아닌 납땜 불량의 중요한 한 종류로 간주되어야 합니다.
2-5-2) 솔더볼 발생 원인
- 플럭스 과다 사용
플럭스가 과하게 도포되면 리플로우 중 급격한 기화가 발생하면서 납 입자가 튀어 올라 솔더볼로 형성됩니다. - 패턴 간격 부족 또는 디자인 미스
인접한 SMD 패드 간 거리가 좁거나, 솔더마스크가 제대로 적용되지 않으면 납이 고정되지 못하고 주변으로 흘러나가면서 솔더볼이 생성됩니다. - 프린팅 불량
솔더 페이스트 도포량이 불균일하거나, 스텐실 두께가 부적절하면 리플로우 시 납이 튀는 현상이 발생하여 솔더볼로 이어질 수 있습니다. - 리플로우 프로파일 부적합
예열 시간이 짧거나, 히팅 속도가 너무 빠르면 납과 플럭스의 동시 반응이 일어나면서 납이 제대로 응집되지 않고 흩어져 버리는 경우가 많습니다. - PCB 표면 오염 또는 습기
PCB나 부품에 남아 있는 수분은 열에 의해 급속히 증발하면서 가스 폭발(Micro explosion)을 유발하고, 이로 인해 납이 튀어 솔더볼을 만들 수 있습니다.
2-5-3) 솔더볼이 유발하는 문제점
- 단락(Short Circuit)
솔더볼이 인접 패드 사이에 붙어 있을 경우, 제품 동작 중 고온 환경이나 진동 등으로 인해 납이 녹아 전기적 단락을 유발할 수 있습니다. - 절연 저하 및 누설 전류
고전압 회로나 RF 회로에서 작은 솔더볼 하나로도 누설 전류나 고주파 특성 열화를 일으킬 수 있습니다. - 컨포멀 코팅(Conformal Coating) 불량 유발
납 알갱이가 표면에 남아 있을 경우, 코팅 막이 고르게 도포되지 않거나 박리, 크랙이 발생할 수 있습니다. - 고객 신뢰성 문제
외관상 불량으로 판단되거나, 잔류 솔더볼이 이온성 오염과 반응하여 장기 고장을 유도할 수 있습니다.
솔더볼(Solder Ball)은 단순히 보기 싫은 납 알갱이가 아니라, 납땜 불량의 종류 중 하나로서 제품의 신뢰성에 직접적인 영향을 미치는 결함입니다.
특히 고밀도 회로나 고속 신호 회로에서는, 작은 솔더볼 하나로도 예기치 못한 신호 이상, 간헐적 단락, 또는 고장 클레임으로 이어질 수 있습니다.
따라서 솔더볼은 단순한 외관 불량이 아니라, 설계, 공정 제어, 세정, 검사까지 전 과정에서 체계적으로 관리되어야 하는 대표적인 납땜 불량의 종류입니다.
납땜 공정에서 발생할 수 있는 납땜 불량의 종류는 생각보다 다양하며, 각각의 결함은 발생 원인과 외형도 다릅니다. 특히 미세 회로, 고속 신호, 고온 환경 등 현대 회로에서는 이러한 결함이 제품 수명이나 안정성에 직접적인 영향을 주기 때문에, 납땜 불량에 대한 선제적 대응과 분석이 필수적입니다.