Contents
1. 생산성 vs 신뢰성, 공정 최적화의 균형
납땜 불량 해결 방법은 전자기기 제조 현장에서 가장 큰 고민 중 하나로, 결국 “어떻게 하면 빠르게, 그리고 동시에 안정적으로 생산할 수 있을까?”라는 질문으로 귀결됩니다.
표면실장기술(SMT)이 고속화되고, 부품이 소형화·고밀도화되면서 생산 공정에서는 이전보다 훨씬 더 정밀한 납땜 품질이 요구되고 있습니다.
하지만 납땜 품질을 높이기 위해 온도 프로파일을 세밀하게 조정하거나, 고가의 플럭스를 사용하거나, 세정 공정을 추가하면 생산 시간이 늘고 원가도 상승합니다.
반대로 생산성만 추구하다 보면, 납땜 불량이 누적되어 신뢰성 문제가 발생하고, 이는 수율 저하나 고객 클레임으로 직결됩니다.
결국 SMT공정에서 중요한 것은 ‘생산성’과 ‘신뢰성’ 사이의 균형을 잡는 것입니다.
특히, 납땜 불량 해결 방법을 단순히 사후 대처가 아닌, 공정 초기 설계 단계에서부터 고려해야 합니다.
이는 단순한 Rework나 수리 공정을 줄이는 차원을 넘어, 제품의 장기적인 신뢰성과 기업의 품질 경쟁력을 결정짓는 핵심 전략입니다.
실제로 생산 속도를 높이기 위해 예열 시간을 줄이거나 체인 속도를 빠르게 설정한 경우, 냉땜이나 브릿지, 솔더볼과 같은 다양한 납땜 불량이 다발적으로 발생됩니다.
이러한 불량은 육안 검사나 AOI에서 통과되더라도, 제품 사용 중 접촉 불량, 간헐적 오작동, 장기 부식 등의 형태로 나타나 장기적으로 브랜드 신뢰성에 악영향을 미치게 됩니다.
반대로 납땜 공정에서 플럭스의 선택, 온도 프로파일의 정밀 제어, 패드 설계 최적화 등 납땜 불량 해결 방법을 사전에 내재화한 설계는, 다소 복잡하고 시간이 들더라도 초기 품질을 안정화시켜 리워크/재작업률을 낮추고, 장기적으로 고객 만족도와 수익성을 함께 끌어올릴 수 있습니다.
특히 납땜 불량 해결 방법은 단일 요소가 아닌, 설계, 공정, 소재, 장비, 검사에 이르는 전반적인 프로세스가 조화를 이루어야 하며, 그 어느 하나도 소홀히 다뤄져선 안 됩니다.
결론적으로 생산성 향상과 신뢰성 확보는 상충되는 목표가 아니라, 서로를 보완하는 관계입니다.
현실적인 공정 최적화란, 납땜 불량 해결 방법을 정량적 데이터에 기반하여 체계적으로 적용하고, 반복 가능한 품질 조건을 공정 내에 표준화하는 일입니다.
이를 통해 기업은 생산성을 유지하면서도 납땜 품질을 확보할 수 있으며, 제품의 수명과 시장 신뢰를 함께 향상시킬 수 있습니다.
- 연관 참조 : 납땜 불량의 종류와 발생 원인 분석
- 연관 참조 : PCB 설계 시 주의사항 1/2, Plane과 부품 배치,노이즈 방사, 다층 기판 등 주의 사항
- 연관 참조 : Rigid-Flex PCB 설계, 3가지 구성, 설계 체크, 주요 공정
- 연관 참조 : 플렉스 PCB 설계 1/2 ,장점 3개, 종류, 설계사양 정하기, 재료 선택가이드
2. 리플로우/웨이브 솔더링 조건 최적화
납땜 불량 해결 방법을 실질적으로 구현하기 위해 가장 먼저 점검해야 할 것은 납땜 공정의 핵심이라 할 수 있는 온도 조건 최적화입니다.
리플로우 솔더링과 웨이브 솔더링은 열을 기반으로 땜납을 용융시켜 접합을 형성하는 공정이지만, 각각의 특성과 변수는 다르며, 이 조건을 잘못 설정하면 다양한 납땜 불량의 원인이 됩니다.
2-1) 리플로우/웨이브 솔더링 조건 최적화
납땜 불량 해결 방법을 효과적으로 적용하려면, 가장 먼저 확인해야 할 것은 온도 프로파일의 정밀 제어입니다.
납땜 공정에서 열 조건은 단순한 설정값을 넘어, 부품과 PCB 간의 접합 신뢰성을 결정짓는 핵심 변수입니다.
특히 리플로우와 웨이브 솔더링 공정 모두에서 다음과 같은 열 구간 설정이 중요합니다:
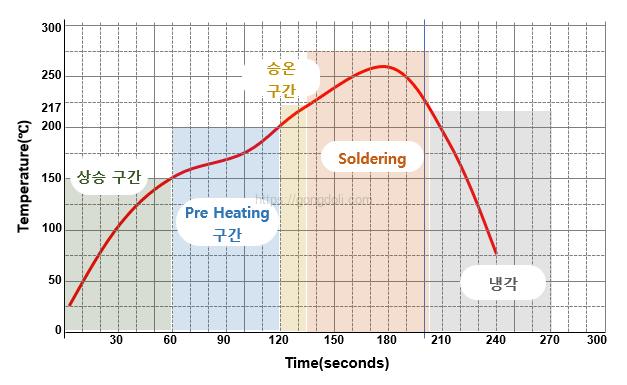
2-1-1) 상승 구간 (Ramp-up)
공정 시작 직후, 기판과 부품의 온도를 천천히 상승시키는 초기 구간입니다.
이 구간에서 온도가 급격히 오르면, 내부 수분이 기화하면서 솔더볼, 보이드, 심한 경우 부품 패키지 파손(팝콘 현상)이 발생할 수 있습니다.
납땜 불량 해결 방법은 상승 속도는 일반적으로 1~3°C/sec 이내로 제한하며, 부품 스펙에 맞춰 조정합니다.
2-1-2) Pre-heating 구간
이 구간은 플럭스 활성화를 유도하고, 기판 전체의 온도를 고르게 분포시키는 역할을 합니다.
기판 중심부가 최소 100~130℃ 이상 도달해야 플럭스가 활성화되며, 그렇지 않으면 젖음 불량, 브릿지, 보이드 등 다양한 납땜 불량의 원인이 됩니다.
웨이브 솔더링에서 특히 중요한 구간이며, 예열이 부족하면 납이 제대로 퍼지지 않아 냉납이나 기공(기포) 발생 가능성이 커집니다.
2-1-3) 승온 구간 (Soak Zone)
플럭스가 완전히 활성화되고, PCB와 부품 전체의 온도를 일정하게 유지하는 구간입니다.
이때 산화막 제거, 납땜 전처리 완료, 열적 평형 유지가 이뤄져야 이후 리플로우 품질이 확보됩니다.
너무 오래 유지되면 산화가 증가하고, 너무 짧으면 플럭스 작용이 충분하지 않아 납땜 불량 발생합니다.
납땜 불량 해결 방법은 Soak 구간은 일반적으로 60~120초 유지하며, 150~180℃의 범위를 유지하도록 설계
2-1-4) Soldering 구간 (Reflow or Wave Soldering)
이 구간에서 실제로 납이 녹아 금속과 결합하는 용융 접합(Melting Joint)이 형성됩니다.
리플로우 솔더링에서는 Peak 온도가 230~250°C 범위에서 형성되며, 솔더 페이스트 종류(무연, 유연)에 따라 다릅니다.
웨이브 솔더링에서는 납 웨이브와의 접촉 시간(2~4초)과 온도 안정성이 핵심입니다.
Peak 온도가 부족하면 냉납, Head-in-Pillow, 과하면 부품 변형, 패드 박리와 같은 심각한 납땜 불량이 발생합니다.
2-1-5) 냉각 구간 (Cooling)
냉각은 단순한 마무리가 아닙니다.
급속 냉각은 납땜부 내에 열응력을 남기고, 크랙(균열)이나 필렛 리프트를 유발할 수 있습니다.
납땜 불량 해결 방법은 일반적으로 4°C/sec 이하의 속도로 냉각하며, 기판이 자연스럽게 상온에 수렴되도록 유도해야 합니다.
2-2) 온도 프로파일이 잘못되었을 때 나타나는 불량 사례
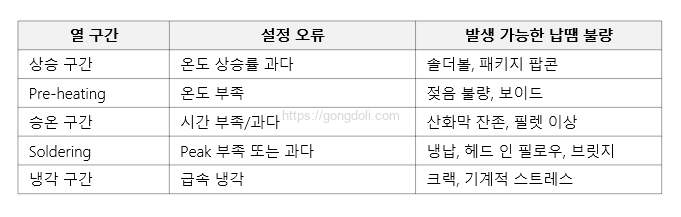
3. 플럭스의 선택과 적절한 사용법
플럭스(Flux)는 납땜 공정에서 필수적인 역할을 수행합니다.
산화물을 제거하고, 젖음성을 향상시키며, 납이 패드와 부품 리드에 잘 퍼지도록 도와줍니다.
하지만 플럭스의 선택이 잘못되거나, 적용 방법이 부적절하면 오히려 납땜 불량의 원인이 됩니다.
따라서 플럭스의 종류, 적용 방식, 그리고 잔류물 처리 방법까지 종합적으로 이해하고 활용하는 것이 중요합니다.
3-1) 플럭스의 종류 및 특성
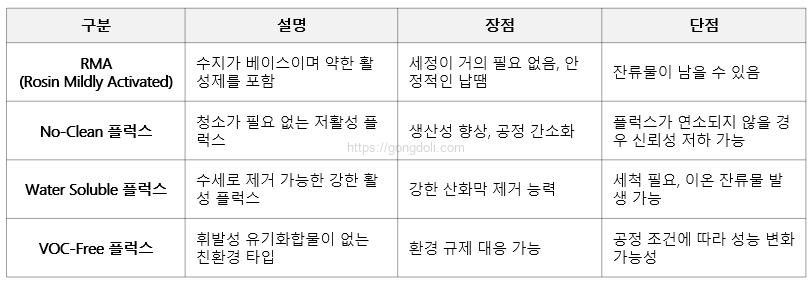
납땜 불량 해결 방법을 고려할 때, 부품과 PCB의 민감도, 후공정 여부, 그리고 신뢰성 요구 사항에 따라 적절한 플럭스를 선택하는 것이 핵심입니다.
예를 들어, BGA나 QFN처럼 플럭스 잔류물이 제거되기 어려운 패키지에는 no-clean 타입을 주의 깊게 적용해야 합니다.
3-2) 플럭스의 적용 방법과 주의점
플럭스는 일반적으로 디핑(dipping), 디스펜싱(dispensing), 스프레이(spray), 브러싱(brushing) 등의 방식으로 PCB에 도포됩니다.
그러나 어떤 방식이든, 적절한 양과 정확한 위치에 플럭스를 도포하는 것이 중요합니다.
- 과도한 플럭스 도포: 솔더볼 브리징, 탄화물 생성, 잔류물 문제로 이어질 수 있음
- 불균일한 도포: 일부 패드에서 젖음성 불량 → 콜드조인트(cold joint) 발생 가능
- 오래된 플럭스 사용: 활성력 저하로 납땜 성능 저하, 수분 흡수 시 기포 발생 가능
납땜 불량 해결 방법 중 하나로, 고정밀 부품에는 정밀 제어가 가능한 스프레이 방식이 선호되며, DIP 부품의 경우는 브러싱 또는 디핑이 효율적일 수 있습니다.
3-3) 플럭스 잔류물의 세정과 관리
플럭스의 잔류물은 시간이 지나면서 이온성 불순물로 변하여 전기적 누설, 부식, 저항값 변화 등을 유발할 수 있습니다.
특히, 고밀도 회로나 고신뢰성 제품(예: 의료기기, 항공, 군수)에서는 플럭스 잔류물 제거가 필수입니다.
- Water Soluble 플럭스: 반드시 세정해야 하며, DI 수를 이용한 클리닝 장비 필요
- No-Clean 플럭스: 기본적으로 세정하지 않지만, 일부 회로에서는 추가 세정이 권장됨
- RMA 플럭스: IPA(이소프로필 알코올) 등으로 세정 가능
세정 여부를 결정할 때는, 납땜 불량 해결 방법의 일환으로 부품 제조사의 플럭스 호환성 자료와 IPC-610/620 등의 기준을 참고하는 것이 좋습니다.
4. PCB 및 패드 설계 단계에서의 예방
납땜 공정에서의 품질 문제는 종종 실제 납땜 과정이 아니라, 그 이전의 설계 단계에서부터 시작되는 경우가 많습니다.
특히 패드의 크기, 간격, 부품의 배열 방식 등은 납땜 불량의 발생 가능성에 큰 영향을 미칩니다.
따라서 설계 단계부터 납땜 공정을 고려하는 것이 납땜 불량 해결 방법의 출발점이라고 할 수 있습니다.
4-1) 패드 사이즈와 간격
패드 크기가 너무 작거나 너무 크면, 납이 제대로 젖지 않거나 흘러넘쳐 브리지(Bridge) 불량이 발생할 수 있습니다.
일반적으로 패드 사이즈는 부품 리드와 납의 흐름을 충분히 수용할 수 있도록 설계되어야 하며, 리플로우 납땜 공정에서는 IPC-7351 표준의 ‘Land Pattern’ 권고사항을 따르는 것이 바람직합니다.
- 너무 작은 패드: 납이 충분히 흐르지 못하고 냉땜(Cold Solder Joint) 발생
- 너무 큰 패드: 납량이 과다해지며 인접 패드와 연결되어 브리지 유발
- 패드 간격 부족: 납의 표면 장력에 의해 인접 패드 간 납이 이어져 단락 발생
납땜 불량 해결 방법 중 하나로 패드 간격이 협소한 경우, 마스크로 패드 간 전부를 개방하지 않고 일부만 오픈하는 방식(“SMD paste mask reduction”)을 활용하면 브리지 방지에 효과적입니다.
4-2) 히트싱크 및 써멀패드 고려
전력 소모가 많은 IC나 FET 등은 패키지 바닥면에 써멀패드(Thermal Pad)를 갖고 있어, 방열판 역할을 하는 PCB 면적에 연결되도록 되어 있습니다.
하지만 써멀패드가 너무 넓으면 리플로우 중 부품이 ‘들뜸(Floating)’ 현상을 보이거나, 납이 고르게 퍼지지 않아 불량이 발생할 수 있습니다.
납땜 불량 해결 방법으로는, 써멀패드 아래에 솔더마스크로 적절한 절연 영역을 주거나, via를 열어 놓고 납의 양을 제어하는 것이 좋습니다.
또한 리플로우 프로파일 상에서 써멀패드가 너무 빨리 가열되지 않도록, 프리히팅 구간을 충분히 확보해 주는 것도 중요합니다.
4-3) 부품 배열의 최적화
부품의 방향성과 배열도 납땜 품질에 직접적인 영향을 줍니다.
특히 웨이브 솔더링의 경우, 납의 흐름 방향과 부품 방향이 일치하지 않으면 그림자(shadowing) 현상이나 납이 끊기는 현상이 발생할 수 있습니다.
리플로우 납땜에서는 부품의 온도용량이 다른 부품들이 인접해 있을 때 승온속도가 달라져 냉땜이 발생하기도 합니다.
납땜 불량 해결 방법 중 하나로, 동일한 온도 특성의 부품끼리 인접 배치하고, 크기가 큰 부품은 중앙보다 보드 가장자리에 배치하는 방식이 효과적입니다.
특히 부품이 몰려 있는 영역은 공정 중 열 분포가 불균일해지므로, PCB 설계 시 발열 집중 지역을 분산 배치하면 리플로우 품질이 향상됩니다.